Scope
Raw-fiber-equivalent trade volume is provided in two formats. Total U.S. textile imports and exports by fiber and by major product group are in one set of tables. The geographic source or destination of the cotton-fiber equivalents of U.S. textile imports and exports are in another set of tables.
The fibers include cotton, linen, wool, silk, and manmade fiber. The product groups include floor coverings, home furnishings, apparel, and an aggregate of intermediate textile products for yarn, thread, and fabric. All trading partners with at least one pound of exports or imports since 1989 are included as a row in the geographic source and destination tables.
These data, combined with data on the utilization of various fibers by the U.S. textile industry, are used to estimate the consumption of fiber products by U.S. households. Apparent U.S. final consumption is measured as the sum of net textile imports in raw-fiber equivalents and domestic industrial utilization of fibers. ERS's calculations are also used by international agencies to estimate global household consumption of cotton and other fibers.
Sources
Trade data at the 10-digit level of the Harmonized Tariff Schedule of the United States (HTS) from the U.S. Department of Commerce's Census Bureau are the foundation of this dataset. While published by the Census Bureau, the data are collected by the U.S. Customs and Border Protection and are ultimately derived from required data on entry papers for imports and on U.S. shippers' export declarations.
ERS has obtained information from contacts in the textile industry to develop factors for conversion to raw-fiber-equivalent weight from textile-product weight, estimating the quantity of raw fiber needed to make each textile product, beginning with the bales of raw fiber opened at the mill. Separate conversion factors for each fiber included in a given product have been created. There are about 7,000 import conversion factors and about 2,000 export factors.
ERS recently updated these conversion factors, taking into account technical change since 1989 and reducing its estimate of unrecyclable waste in cotton yarn production. See Highlight: Textile Trade Conversion Factors Revised Down for Cotton.
Updates
Data are updated annually.
Conversion Factors
Two examples illustrate how fiber-equivalence is determined. The foundation of USDA's conversion factors is information on five relevant product characteristics for each textile product listed in the HTS. From industry contacts, ERS determined for each product:
- The total fiber share of the product's weight (Perfib),
- Cotton's (or another fiber's) share of the product's fiber content (Blend),
- Waste resulting from yarn manufacture (Yarnwaste),
- Waste from trimming during weaving and knitting fabric (Fabtrim), and
- Cutting loss in apparel and other finished product operations (Cutloss).
The first example illustrates on a per-garment basis how these characteristics are used to estimate fiber equivalence. The product examined is HTS 6110909026, Sweaters, women's, other fibers, subject to cotton restraints (fig. 1), with the numbers in parentheses corresponding to each of the above characteristics:
Lacking buttons or zippers, the product is (1) 100 percent comprised of fiber, and, on average, is (2) 45 percent cotton. Therefore, 1 kilogram of sweaters includes 450 grams of cotton fiber. However, assuming that (3) 5 percent of the cotton fiber used to spin the sweater's yarn is lost, and given (4 and 5) further losses in knitting and assembling, a waste factor of 21 percent is applied. The result is a total of 545 grams (450 grams x 1.21) of raw cotton needed to produce 1 kilogram of this product.
For this product, each sweater weighs 403 grams, on average. Therefore, based on the product characteristics, the per-sweater cotton-fiber equivalence is 219 grams. Figure 1 shows the same calculation with a slightly different order; the per-garment weight is used as the starting point.
A second example is used to focus on the most technical segment of the calculation of fiber equivalence: the role of waste in the textile supply chain. Table 1 illustrates the calculation of waste at each stage of the process of producing a textile product and again shows how the information about the composition and production of a good is brought together into a single conversion factor.
1. Perfib | 2. Blend | 3. Yarnwaste | 4. Fabtrim | 5. Cutloss |
---|---|---|---|---|
Fiber's share of product weight | Cotton's share of fiber in product | Fiber lost in yarn production | Yarn lost in fabric production | Fabric lost in product construction |
100 | 10 | 5 | 3 | 0 |
Source: ERS calculations based on industry information. 1HTS5112909010: woven fabrics of combed wool/combed fine animal hair mixed mainly or solely with cotton. |
Yarnwaste, Fabtrim, and Cutloss represent the three product characteristics used to calculate waste in the production of textile products. Note that the term "waste" is not meant to imply this fiber, yarn, or fabric is all irretrievably lost. Some waste is recyclable and utilized by other industries. However, such waste is incorporated into nontextile products. Therefore, from the perspective of deriving estimated fiber use from data on shipments of textile products, the fiber is lost, and a waste factor is needed to account for it. The goal of these estimates is to capture fully the initial demand for fiber. Accounting for waste is a more efficient approach than working only with the product weight of textiles and then taking on the additional task of estimating the fiber share of nontextile products that might have been derived from textile waste.
The waste estimates are each subtracted from 100 percent and the inverse of this difference calculated. This converts the estimated amount of loss at each stage of the product's production (e.g., 5 percent for yarn production) into the estimated units of input needed to create a unit (e.g., 1 kilogram) of output. For example, yarn spinning:
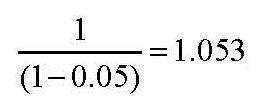
The equation above indicates that 1.053 kilograms of cotton fiber are consumed to produce 1 kilogram of yarn.
This subtraction and inversion is also applied to fabric production (Fabtrim) and garment production (Cutloss). The product of these three inverted factors is the volume of fiber needed to create 1 kilogram of the textile portion of the product in question.
The product of the inverses must also be multiplied by the "Blend" factor, which represents the percentage of cotton content in the commodity. Also factored into the equation is the fiber composition of the commodity, accounting for buttons, zippers, and other nonfiber-based components ("Perfib"). The product of these components is the conversion factor for mill-use equivalents, by weight, per weight of product exported or imported. Below is the conversion factor for mixed fabric:
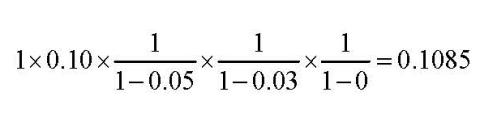
Products
ERS converts the above information about each of the 9,000 products in its database into a conversion factor to estimate the raw-fiber equivalent of U.S. textile product trade in that product for each fiber. ERS publishes these estimates in summary form, combining the estimates for individual products into product groups like "apparel."